

Interior solutions and custom
made furniture production


Fitsout
SUCCESS STORY

Overview
Fitsout is a greenfield investment, a new company founded in 2018. Same year, one of the largest (20,180 m2) modern custom-made furniture factories in Europe was built and launched.
Fitsout clients are international well-known brands operating a network of retail stores, hotels, offices, restaurants, exclusive design houses. Those are large and complex projects whose solutions are not repeated. And it‘s a completely different business than serial or mass production.
A lot of attention was paid to team building. The Success story company has with more than 20 years of experience in creating tailored world-class fit out solutions to customers.
These professionals fully understood the importance of the design and information preparation process for production. Therefore, great attention was paid to its construction and tools.
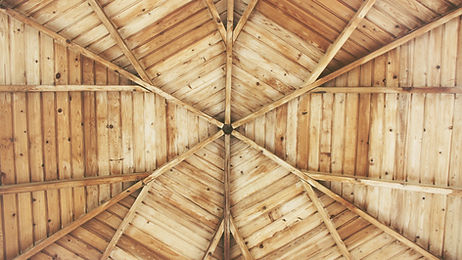
Challenges
Working with branded stores, large projects, remote geography - all this poses complex challenges to the company's production information cycle process:
Time-to-Manufacturing
There are no standard products in bespoke production. As a result, each order requires individual design and generation of information for production. This process, unlike mass production, takes a significant part of the lead time in bespoke production.
Deadline Pressure
The interior of the store is installed last - after construction, utility networks, electrical works, etc. Very often, those parts are delayed and the interior designers have less and less time to implement their part, because delaying the deadline means losses for the shop. As a result, interior designers are under enormous deadline pressure and it is critical for them to be able to complete an order quickly and, more importantly, error-free.
Non-Traditional Materials
Fitsout's customers are brand stores. Exclusive designs are used in such stores - complex structural solutions and very diverse, non-traditional materials.
React Quickly
Usually, a number of changes occur during the course of such projects. Which is why it is important for Fitsout to be able to react quickly to it and adjust the projects accordingly during the project implementation.
Requirements
In order for Fitsout to cope with the aforementioned challenges, a solution was needed which:
Any Complexity Designs
Would allow designing furniture and other interior details of any complexity and geometry without limitations
Any Materials
Various materials could be used in the design - metal, glass, plastic, stone, etc. And that this is automatically reflected in the specifications without additional manual processing.
Design Fast
Would allow to quickly design from scratch and prepare information for production.
Change Data
Would allow easy changes in the design and automatically generate the necessary data for production.
Systems Integration
Would ensure the seamless transfer of information to other IT systems of the company - ERP,specialized CAM systems (CutRite, Woodwop, etc.).
Teamwork
Would allow teamwork, so that designers of different parts - wood, panel, metal, etc. - could work onone project.

The management of the company set the goal of creating an information cycle for bespoke production, which would be as close as possible to the information cycle of mass production in terms of speed and efficiency.
Solution
After detailed evaluation, Autodesk Inventor and Woodwork for Inventor solution were selected.
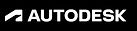
Autodesk Inventor provides all the capabilities of a modern parametric 3D system, allowing you to design furniture and interiors of any complexity, and quickly modify projects.


Woodwork for Inventor turns Autodesk Inventor into a powerful and efficient tool for furniture makers, giving it all the functionality needed for furniture design:
01
Any Materials
Made it possible to work with any materials and automated the calculations of the dimensions of the time-consuming workpieces and the required quantities of materials,
02
Gives Data
Provides this information in a suitable form for transmission to further information chains for production management,
03
Automated Process
Ensures automated preparation of drawings and generation of CAM programs.
Since non-standard furniture is being designed, it was impossible to speed up the design using pre-prepared templates. As a result, methodologies have been developed to design quickly from scratch and make changes to such a structure painlessly.
Customization of the information generated by Woodwork for Inventor for production was carried out to meet the requirements of the company's internal processes.
Two-way communication with ERP was established with the company's programmers. From the ERP system, the information about the materials needed for the construction of the product components is used directly. Meanwhile, Woodwork for Inventor automatically generates specifications about the product being constructed, which are imported into the company's ERP system.
Jonas Stragis, Fitsout CEO
We needed unique tools for designing and preparing information for production. We had two alternatives - either to create such tools ourselves or to look for solutions on the market and adapt it to our specifics. We chose Autodesk Inventor and Woodwork for Inventor. Working together, the Woodwork for Inventor team adapted them to our processes. This allowed us to save both the time and cost of building and polishing our own system, as well as the costs of subsequent support.
This solution helps us to fully utilize available intellectual and production capabilities, thanks to which we can realize our unique know-how. In combination with the processes, we have built, these tools allow us to quickly and qualitatively launch complex orders into production, which makes it easier to manage the timely realizations of orders.
As the business expands and circumstances change, new tasks arise. We continue to work with the Woodwork for Inventor team to adapt the system to new circumstances and maximize the benefits created by this system.
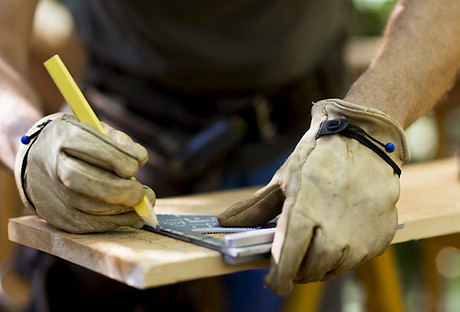
Results
Since Fitsout uses a single solution from the start, there is no baseline to measure the change institution. However, it is possible to name the qualitative parameters in comparison with the situation if this a solution was not applied.
System Design Power
Due to the fully utilized capabilities of Autodesk Inventor, the company is able to design products of the highest complexity. Thanks to Woodwork for Inventor, this power is applied to furniture design.
Speed
Woodwork for Inventor automates routine designer operations for preparing information for production - specifications, drawings, and CNC programs. General practice shows that if this work is not automated, it takes up to 70% of their working time for constructors. With the most modest estimates, it could be said that Fitsout saves 20% - 30% of constructors' work time compared to the case if Woodwork for Inventor was not used.
Quick Changes
The parametric design system allows you to conveniently make changes during the course of the project and adapt to the circumstances. And thanks to automated data generation and integrated data transmission, it is done quickly. This allows the company to respond quickly and at minimal cost to changes occurring during the course of the project.
Teamwork
The products created by Fitsout consist of different parts - part of cabinet furniture, part of metal constructions, part of glass constructions, electrotechnical part, etc. The design of these parts requires different competencies. An opportunity has been provided for the designers of all parts to work in one context, which greatly saves time in coordinating those parts with each other and avoiding errors.
Error Elimination
Automated generation of information from the model eliminates human error. Eliminating such errors greatly saves the time spent on their correction and reduces the cost of damaged materials.
Integration
Thanks to the integration with ERP, the company saved additional human resources that would have processed the information generated by Woodwork for Inventor and brought it to ERP. This means cost savings, reduced data transfer time, and elimination of human error.
Synchronization
Thanks to ERP's use of material information in design, the need for a separate furniture material database for the CAD system is avoided. This saves additional IT resources and efforts for synchronizing those databases and eliminates the occurrence of errors due to the existence of two different information sources.
